Published:
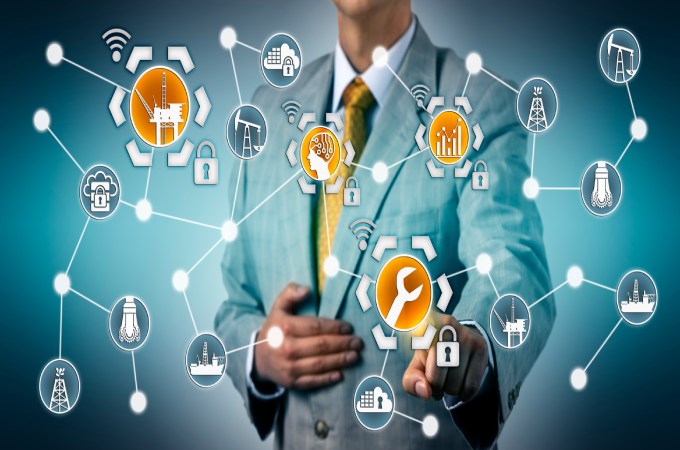
Digitalisation is already playing an important role in the energy industry, but more needs to be done for the sector to truly embrace the future of business.
The world has witnessed significant advancements in technology, which combined with the reduced cost of digitalisation. is being embraced by every industry at various levels. In the last two years, the world has realised the power of digitalisation and connectivity even more than before. And the oil and gas sector is not far behind in realising that.
A report by DHL states that digitalisation will continue to play a significant role in transforming the oil and gas sector, potentially unlocking $1.6 trillion to $2.6 trillion worth of revenue by 2025. While the industry lags in technology adoption due to many constraints including regulatory frameworks and data standardisation, there are several changes that the industry has adopted.
For example, transformative strategies, digitised processes, energy trade. and risk management [ETRM], customer relationship management [CRM], enterprise resource planning [ERP]. document management systems (DIAS), and the digitisation of legacy systems, artificial intelligence [Al] and machine learning [ML]. Taking a step ahead, it is evident that industry 4.0 is already here. According to the Facts and Factors market research report, the worldwide industry 4.0 market size and share revenue is expected to grow from $70 billion in 2019 to reach $210 billion by 2026, at 17% annual CAGR growth during the forecast period of 2021-2026.
The significant impact of industry 4.0 is yet to be seen in the sector as it will undoubtedly change the course of how it has worked in a legacy manner. For example. when organisations adopt the solutions provided by industry 4.0, they can reduce costs, minimise the risks and human error, decrease the design costs and focus on enhancing the efficiency of processes. The systems also become more flexible and efficient, with possibilities far personalisation. Moreover, according to McKinsey, effective use of digital technologies, such as cloud, the Internet of Things [IoT], mobility, artificial intelligence (Al], virtual reality [VR], big data. and analytics could cut capital expenditure by up to 20%. In this backdrop, Dr Ismail Labed, Director of Studies Petroleum Engineering at the School of Engineering, Geoscience, Infrastructure and Society at Heriot-Watt University Dubai, delves into the role of industry 4.0 in the oil and gas sector.
The oil and gas supply chain
The oil and gas supply chain can benefit exponentially through the digitalisation of certain processes. For example, the usage of unmanned aerial vehicles such as drones can significantly disrupt the industry by removing the need for manual inspections of the pipelines in difficult-to-access locations. These can also prove beneficial in dangerous situations such as gas leaks and support early detection through instant data collection and transfer. Additionally, the usage of data integration technologies and information sharing across the supply chain and support organisations to adjust production levels in real-time. based on inventory data from storage facilities, rate of distribution, and forecasted demand. Furthermore, cloud computing and loT are two key technologies that can create networks of connected tools and personnel at every oil and gas supply chain stage. The two main benefits of this are remote management of workforces and real-time monitoring of processes and equipment. Finally, a digital overview of the entire supply chain model links complex networks in a way that provides a 360-degree understanding of the value chain to be visualised, analysed and optimised in real-time.
The exploration stage
3D seismic imaging forms a critical part of oil and gas exploration. It allows companies to discover potential oil and gas accumulations and collect data to evaluate complex surface formations. Time lapse, 4D modelling is used to support seismic imaging as it helps integrate production data and to map changes in the oil and gas saturations in a particular reservoir. By combining geoscience data standardisation, high-performance computers and advanced algorithms, companies are developing new workflows to interpret and analyse seismic data through machine learning techniques.
Additionally, drilling data management is another technological advancement that is being integrated into the oil and gas sector. According to reports, the drilling data management systems market has undergone substantial growth in recent years, with the market size anticipated to reach $8.38 billion by 2024 and growing at a CAGR of 6.32% from 2017-2024. Furthermore, recent innovations in drilling tools are also generating large amount of data during drilling operations.
Tools such as logging whiledrilling (LWD) and measurement while drilling (MW)transmit various data to the surface in real-time. Also, optical fibres combined with various sensors are now being used in well tubular to record different parameters such as fluid pressure, temperature, and composition during oil and gas production.
The finished product
Refining is the last stage of oil and gas production before it is distributed to customers. Also known as downstream, refining generally does not involve any interference from technology. However, using technologies such as hybrid models, closed-loop production - to avoid contamination, optimisation - to make near term commercial decision, and predictive analytics can significantly support oil and gas organisations in enhancing their assets, achieving carbon mitigation and reducing site-wide energy usage through programmatic technology.
As such, hybrid models make it far easier to benefit from refinery-wide planning, scheduling and optimisation. These more accurate asset-wide models are key in defining the integrated oil-to chemicals processes that can further improve operational excellence across the value chain. Also, digitising maintenance of refineries can reduce cost and ensure real-time data on high-risk and potentially problematic areas. Sustaining utilisation through routine maintenance procedures is vital to refining profitability. Although large maintenance turnarounds are often delayed during periods of high asset utilisation, refineries must keep up with routine maintenance in order to prevent unplanned downtime.
The global oil and gas industry is on the threshold of adopting significant technological advancements, while some are already in place, others are still being explored. The sector will benefit largely from digitisation and industry 4.0. However, to achieve success, it is also dependent on governments, organisations and academia to work closely to build systems and processes significantly support sustainability in the industry. As for digitisation also, the next generation will need to be academically and practically prepared to step into what is next for the industry.